Blog entry by Bruce McPherson
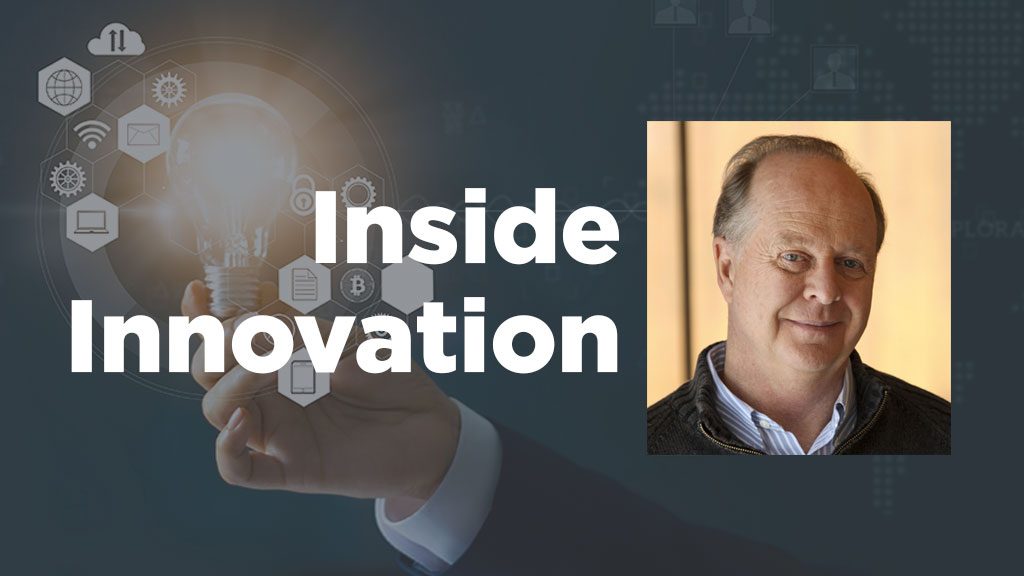
The use of drones on construction sites increased by 239 per cent from 2017 to 2018, according to DroneDeploy, a leading drone software platform. This rapid growth is part of a global commercial drone market that Goldman Sachs estimates will be worth $100 billion this year.
Drone usage is exploding for the simple reason that it can provide more detailed information, job tracking and communications at costs that can’t be met on the ground. DroneDeploy cites the example of Rogers-O’Brien Construction, a leading general contractor in Texas. The company reportedly saved thousands of man-hours, increased efficiency, avoided costly budget overruns, and reduced inspection costs by 99 per cent.
Yet, moving drone integration from concept to execution is a multi-step process requiring commitment. Many companies remain parked on the sidelines because they lack a plan for moving forward.
Joao Antunes, writing on behalf of the AEC-NEXT Technology and Apps Conference (June 3 to 5, 2020), says any consideration to initiate a corporate drone program relies on several factors. It begins with a detailed assessment to determine whether drones are, in fact, the right tool to solve the company’s data-gathering problem.
Skyward, a Verizon company offering drone consultancy to various industries, suggests that company insiders proposing the adoption of drones first need to secure a buy-in at the executive level. This is best achieved by finding what Skyward calls “an initial use case” — a pilot project — that can measure the benefits drones could provide.
Management’s decision whether to then move forward, and on what basis, will be based on a thorough examination of costs versus benefits. Many questions need to be asked:
- Would drone technology result in a competitive advantage?
- What would the standardized procedures accompanying the use of drones look like?
- How would the data gathered by the drones be analyzed?
- Can that data be shared among various project team members and partners without severe disruption of current protocols?
- What are the potential project risk reductions?
- What are the costs of postponing the decision to adopt drones until next year?
- Most importantly, should the company invest in its own program or outsource its aerial monitoring needs?
Outsourcing to third party providers makes sense in specific circumstances, says Antunes. “These types of companies can be leveraged for their existing infrastructure or expertise, which can contribute to cost savings. They may be especially useful for unique or one-time projects that would benefit from drone use but may not (yet) be worth investing in a suite of new technology for the construction company to own.”
If the company chooses instead to bring a drone program in-house, the “suite of new technology” referred to by Antunes requires a significant investment of resources and strict adherence to government regulations.
First, drone pilots working on or near construction sites must pass Transport Canada examinations in order to hold a Pilot Certificate for Advanced Operations. Several independent facilities offer the required pilot training courses should current unlicensed employees be interested. Alternately, community colleges that provide drone training programs might be a source for hiring pre-qualified pilots.
Secondly, a decision must be made regarding which of the many types of drones to purchase — multi-rotor, single rotor, or fixed-wing. Which type of sensors best meet company needs and budgets? Are cost-effective photogrammetry sensors enough, despite limitations due to flight visibility? Or do project needs call for more expensive Lidar sensors, capable of creating highly accurate 3D maps in all weather conditions and no matter what ground cover conditions exist? Whatever hardware choices are made, the drone software must integrate smoothly with the company’s workflow processes and BIM platforms.
Today’s drone mapping and monitoring technologies are revolutionizing the industry. They offer construction companies powerful ways to increase productivity through enhanced project communications, time and cost efficiencies, and improved site safety. The question is not just whether to buy or hire; it’s “How long can you hold out?”
By John Bleasby